From Concrete international, August 2009, pages 35-38. Reproduced with permission of the American Concrete Institute (www.concrete.org).
Stephen J. Hayde: Father of the Lightweight Concrete Industry
From the remnants in a brick cull pile, lightweight aggregate was developed
By T.W. Bremner and John Ries
Builders have long recognized the importance of reducing the density of concrete while maintaining its durability and strength. The Romans used natural deposits of vesicular aggregates such as pumice and scoria as the aggregates of choice for their structures—even when normal density sand and river gravel were readily available. Examples still in place today include the piers at the Port of Cosa, built on the west coast of Italy shortly after 273 BCE,1 and the 50 m (164 ft) diameter dome of the Pantheon, built in 128 CE by Hadrian. In the Pantheon, the intrinsic variability of natural vesicular aggregates was circumvented by hand-sorting them according to density, allowing the density of the concrete to be reduced as the height of the dome increased and stresses decreased.2
The variability of natural deposits of volcanic aggregates, however, remained a challenge for almost 2000 years until it was solved by Stephen J. Hayde (Fig. 1), the American-born son of Irish immigrants from Tipparary. His parents, Patrick Joseph Hayde and his wife Bridget, arrived in New York with their young family, possessing a letter from Ireland stating Patrick had “credentials,” which no doubt advanced his cause for he readily found work with the government as a contractor/civil engineer repairing buildings and bridges in the West.3 Stephen Hayde was born in 1861 at Keokuk, IA, and worked with his father from boyhood in Kansas City, MO. After a few years spent in San Francisco, CA, Hayde returned home where he became well known as a brick maker and building contractor, constructing such impressive brick buildings as the Missouri Building at the Chicago Exposition and the Loretta Academy.4
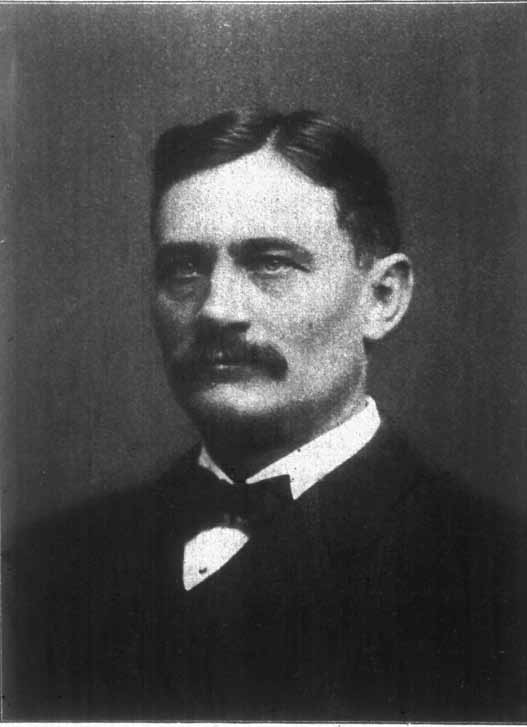
Fig. 1: The inventor
Producing Brick
Using the down-draft beehive kilns of that time, brick making was a rather inefficient process, as the temperature varied greatly within the kiln. After a particular load was “burned,” the product had to be hand sorted. “Hardburned” bricks were suitable for exterior use because of their resistance to rain penetration as well as the effects of freezing and thawing. “Salmon” bricks (so-called because of their pink color) were not thoroughly burned but were suitable for interior use.
A third category, “bloaters,” went into a cull pile and represented a significant financial loss to the producer. These were bricks located close to the heat source in the kiln that were heated too rapidly for the evolved gases within the clay to dissipate, and thus expanded by more than a third of their original size. Bricks produced with certain clay deposits retained this distended shape upon cooling, resulting in a vesicular internal structure with essentially unconnected voids surrounded by a hard, impermeable ceramic-like matrix.
Stephen Hayde had an inventive and resourceful mind. He saw value in crushing the cull pile to size and incorporating it in a concrete mixture. This, he felt, could provide a consistent way to produce a lightweight concrete of substantial strength and durability. In a letter to his nephew George dated October 7, 1914, he recounted how he had “burned” some material at the Ocean Shore Iron Works in San Francisco. He specifically mentioned that “some of the material is so light it floats in water.” He also mentioned that his final product didn’t have planes of weakness. Along with the letter, he sent samples of the material he’d prepared.
Producing Aggregate
Hayde was so sure of the virtues of his new material that he engaged a patent attorney on January 29, 1914. U.S. Patent No. 1,255,878 was subsequently issued in Hayde’s name on February 18, 1918.5 The patent covered argillaceous material and specifically mentioned “special clay, slate, and shale rock,” implying that not all argillaceous material is suitable, and that the product must be heated to a temperature of 1220 °C (2228 °F) for about 2 hours. In the text of the patent, Hayde stated, “my invention relates to the manufacture of brick, tile, terra cotta, and like molded articles.”6 After returning from San Francisco to Kansas City, Hayde took charge of the Flannigan-Zeller Brick Company, where he had access to brick kilns as well as access to rejects from the brick making process (bloaters) to crush to a size suitable for doing research on low-density concrete.
In a conversation with Warren Allen, Hayde’s assistant Lou Harris explained how they had experimented with balls of clay that were placed at various locations in the brick kiln. Their goal was to identify the correct time-temperature regime to achieve properties in aggregates that could be used in a concrete mixture to produce optimum properties in concrete. In 1917, his tests showed that a rotary kiln could be used to economically produce expanded shale, clay, and slate in large quantities with properties identical to those being produced today.5
Producing Ships
Hayde’s ability to efficiently produce large quantities Concrete international/ august 2009 37 of lightweight aggregate ideally suited to making highstrength, durable, and low-permeability concrete was timely, as it was met with urgency in the marine shipping industry brought about by the submarine warfare of World War I. As a construction material for boats, portland cement concrete probably dates from 1848, when JeanLouis Lambot built a rowboat for use in a pond on his estate in Miraval, France.7 With a hull thickness of 30 to 40 mm (1.2 to 1.5 in.), a length of 3.6 m (11.8 ft), and a beam of 1.35 m (4.4 ft), the boat was a success. Other than a hole in the bottom that caused it to sink, it was found in good condition some 100 years later when it was excavated from the mud and exhibited at a concrete conference in Paris. The first ocean-going concrete ship was constructed in 1917. With a displacement of 400 tonnes (440 tons) and a length of 26 m (85 ft), the Norwegian ship Namsenfjord showed marine designers the possibilities and limitations of using normalweight concrete as a material.8
Although vesicular volcanic aggregates had been tried and found capable of reducing the dead weight of ships to manageable levels, the intrinsic variability of the deposits of aggregate were such that the required high strength could not be obtained on a consistent basis. Hayde was a patriotic individual, and with the recognition that his soon-to-be-patented product could help in the war effort, he offered it free of charge to the government for the duration of the war, provided that the Haydite, the name given to his lightweight aggregate product, was manufactured by the government and not an independent contractor.9
His offer was made in a letter dated February 18, 1918, to the Director of the Department of Concrete Ship Construction, U.S. Emergency Fleet Corporation, Washington, DC. The response was provided on March 6, in a letter signed by R.G.J. Wig as Chief Engineer and initialed by C.W.B. (Carl W. Boynton). The letter expressed interest in the “burnt clay as a concrete aggregate in concrete with boat construction and anticipated that the material can be developed to a point where it will give us the required strength, and at the same time reduce the weight of the concrete materially.” Subsequent testing verified that Haydite could be used to produce 28 MPa (4000 psi) concrete with a density of 1697 kg/m3 (106 lb/ft3).
With Hayde’s experience making a high-quality lightweight aggregate using a rotary kiln, it was surprising that the first ship built by the Department of Emergency Ship Construction was constructed using aggregate from the much less efficient down-draft beehive kilns in Birmingham, AL. Sufficient material was produced to supply concrete for the 272 tonnes (300 ton) Atlantis, launched in December 1918. The second concrete ship was the Selma, with a length of 132 m (434 ft), a beam of 13 m (43 ft), and a full-cargo draft of 8 m (26 ft). The ship’s hull was 127 mm (5 in.) thick on the bottom and 100 mm (4 in.) thick on the sides. Cover over the reinforcement was only about 16 mm (5/8 in.). The aggregates used to construct the Selma were made by the Atlas Cement Company in Hannibal, MO, using the rotary kiln method. A total of 6670 tonnes (7350 tons) of expanded aggregates were shipped to the Fred T. Ley Company, the operator of the government shipyard in Mobile, AL.
The good performance of rotary-kiln-produced lightweight aggregate when used for concrete ship construction was not missed by government employee Carl Boynton, who proceeded to arrange for a patent to cover what was essentially covered in Hayde’s patent. This is especially surprising in that Boynton had expressed to Appo, one of Hayde’s associates in the Haydite company, that “the process…was entirely outside his knowledge of burning materials and burning processes.” On May 7, 1928, at the Court of Appeals of the District of Columbia, a decision was rendered that the court was “convinced that Boynton derived his knowledge of the invention from Hayde, and that Hayde is entitled to the award of priority.” A key piece of evidence in the case was the letter Hayde had written to his nephew George. A petition for a rehearing was denied on June 1, 1928. Unfortunately, that victory came some 16 days after Hayde died when traveling by rail from Montreal to Kansas City.
Relics
The Atlantis lays a wreck in pieces at Crystal Beach on the southern tip of Cape May, NJ. One of the authors visited the wreck about 1980 and found the concrete of very poor quality. The Selma was scuttled decades ago off the coast of Galveston, TX. One of the authors visited the Selma in 1985 and observed that the concrete was generally in excellent condition, and the imprint of the form boards could still be clearly seen—even at the water line. As is the case of the concrete ships from World War II, the main deck shows distress mainly due to improper concreting practice. Nevertheless, the concrete was in generally good condition and shows what can be expected of concrete made with rotary-kiln-produced lightweight aggregate.
Producing a legacy
Hayde’s research, which began about 1897, had established by 1917 the basic parameters for aggregate production that led to our modern lightweight concrete industry. The temperature regime and degree of expansion of the aggregates has remained unchanged over the years. It is a great benefit to modern designers that they can look back with confidence at a track record of nine decades of good performance with this essentially unchanged product, invented and brought into commercial production by Stephen Hayde. In other words, Hayde got it right the first time with his product registered under the name of “Haydite.”
Although Hayde was a successful building contractor and financier who was a director of the Bankers’ Trust Company, there was no record found that he profited greatly from his three decades of research—even though he virtually developed the lightweight concrete industry single-handedly. In contemporary records, however, he is described as a businessman of enterprise and determination, “who has contributed in substantial measure to the architectural adornment of the city and who during labor troubles took a stand that won for him the lasting gratitude of the unions.”4
Hayde’s patent lived on well after his passing. Upon his death, patent and manufacturing rights went to his widow, Kitty Hayde (formerly Katherine M. McFarrelly). When Kitty became old and mentally infirm, the rights came into the possession of her companion, William R. Stanley, a financier. Prior to his death at the height of the Depression, Stanley sold the patent rights to others. Although the patent remained in effect until 1947, Stephen Hayde’s relatives gained nothing from it—a fact that riles the extended family to this day.10
References
1. Bremner, T.W., and Holm, T.A., “High Performance Lightweight Concretes,” Proceedings of the Second CANMET/ACI International Symposium in Advances in Concrete Technology, SP-154, V.M. Malhotra, ed., American Concrete Institute, Farmington Hills, MI, 1995, pp. 1-80.
2. Bremner, T.W.; Holm, T.A.; and Stepanova, V.F.,“Lightweight Concrete—A Proven Material for the Millennia,” Proceedings of Advances in Cement and Concrete, S.L. Sakar and M.W. Grutzeck, eds., University of New Hampshire, Durham, NH, 1994, pp. 37-51.
3. Whitney, C.W., Kansas City, Missouri: Its History and Its People 1800-1908, V. 3, 1908, pp. 134-135.
4. Kansas City Architect and Builder, V. 20, No. 11, Nov. 1905, p. 12.
5. Hayde v. Brynton, 26F.2d 987 (D.C. Cir. 1928).
6. U.S. Patent No. 1,255,878 (issued February 12, 1918).
7. Fisher C.W., “Lambot’s Boat—A Personal Discovery,” Concrete, Nov. 1967, pp. 380-382.
8. Bremner, T.W.; Holm, T.A.; and Morgan, R.D., “Concrete Ships— Lessons Learned,” Proceedings of the Third CANMET/ACI International Conference on Concrete in Marine Environment, SP-163, V.M. Malhotra, ed., American Concrete Institute, Farmington Hills, MI, 1996, pp. 151-170.
9. Kansas City Star, June 11, 1928.
10. Conversation with John Hayde of Kansas City, MO, a descendant of Stephen J. Hayde’s brother.
T.W. Bremner, FACI, FCSCE, is Professor Emeritus and Honorary Professor of Civil Engineering at the University of New Brunswick, New Brunswick, Canada. He is Past President of the ACI Atlantic Chapter. He received the ACI Cedric Wilson Award in 1988 and ACI Construction Practice Award in 1989, and is Past Chair of ACI Committees 122, Thermal Properties and Performance of Concrete and Masonry Systems, and 213, Lightweight Aggregate and Concrete.
ACI member John Ries is President of the Expanded Shale, Clay and Slate Institute, Salt Lake City, UT. His committee memberships include the ACI Board Advisory Committee on Sustainable Development and ACI Committees 211, Proportioning Concrete Mixtures; 301, Specifications for Concrete; 302, Construction of Concrete Floors; and 308, Curing Concrete.